IAC™ Intelligent Arc Control - proces pro snižování rozstřiku a vneseného tepla při zkratovém přenosu
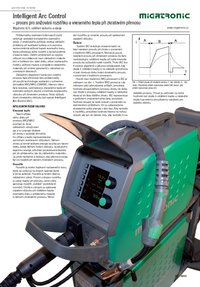
Patentovaná funkce stroje Sigma Galaxy pro MIG/MAG svařování studeným obloukem. Garantuje stabilní oblouk, minimální rozstřk, dokonalý průvar kořene a možnost svařování i při široké kořenové mezeře.
Migatronic A/S, oddělení výzkumu a vývoje
Problematika svařování kořenových partií ovlivňuje výsledek kompletního svarového spoje. Z praktického pohledu existují základní problémy při svařování kořene, a to zejména nerovnoměrná velikost kapek svarového kovu, která způsobuje velký rozstřik a nerovnoměrně vnesené teplo. Dalším problémem je vysoká citlivost na vzdálenost mezi základním materiálem a hořákem tzv. výlet drátu, sklon svařovacího hořáku, velikost mezery a propálení základního materiálu při změně parametrů v závislosti na zmíněných faktorech. Základním stavebním kamenem nového procesu byla eliminace této problematiky při použití technologie svařování v ochranné atmosféře MIG/MAG (GMAW).
Hlavním cílem byla redukce, optimalizace vneseného tepla při svařování tenkých plechů a kontrola svařovacího oblouku při zkratovém procesu. Nový způsob řízení zkratového oblouku byl nazván Intelligent Arc Control (IAC™).
INTELIGENTNÍ ŘÍZENÍ OBLOUKU
Vnesené teplo
Tavení přídavného drátu při procesu MIG/MAG pochází ze dvou základních zdrojů energie - a to: energie dodané při zkratu v podobě ohmického ohřevu a teplo reprezentované samotným svařovacím obloukem. Během zkratu je téměř veškerá energie využita pro tavení drátu, avšak během hoření oblouku vyzařujícího tepelnou energii, přechází produkovaná teplota jak do přídavného, tak do základního materiálu. Je proto nezbytné a žádoucí, aby přenos energie byl co největší při daném zkratovém procesu.
Rozstřik
Rozstřik je tvořen kapkami roztaveného kovu, které se uchycují na krajích svarové lázně a liší se velikostí. Rozstřik je tvořen dvěma základními zdroji. Prvním zdrojem rozstřiku je odraz kapky při přenosu, tento zdroj generuje rozstřik „kuliček“ podobných rozměrů. Druhým zdrojem je opětovné
zapálení oblouku při oddělení kapky svarového kovu z přídavného materiálu během zkratového procesu. Množství rozstřiku je úměrné proudu při opětovném zapálení oblouku.
Řešení
Systém IAC™ redukuje vnesené teplo na bázi navýšení proudu při zkratu v porovnání s tradičním MIG procesem. Nicméně pouze navýšení proudu při zkratovém procesu by bylo nedostačující, oddělení kapky při vyšší intenzitě proudu by způsobilo vyšší rozstřik. Proto IAC™ tvoří soubor algoritmů s přesnou předpovědí, kdy dojde k oddělení kapky a na základě vyhodnocení pak zkracuje dobu trvání zkratového proudu v porovnání s tradičním procesem. Rozdíl mezi tradičním MIG procesem a IAC™ je zobrazen na obr. 1. Tradiční MIG proces je zde zobrazen jako přerušovaný průběh, proudová hodnota stoupá během procesu zkratu do doby, než dojde k procesu oddělení kapky a následně klesá až do fáze dalšího zkratu. IAC™ reprezentuje v grafickém znázornění plná čára, proudová hodnota stoupá na vyšší úroveň v porovnání se standardním průběhem, tím je zabezpečena dostatečně velká energie v této fázi. Aby nedošlo k rozstřiku, proudová hodnota klesne na nízkou úroveň, ale jen do takové míry, aby nedošlo k nestabilitě procesu. Proud je udržován na nízké hodnotě než dojde k oddělení kapky a následně dojde k jemnému proudovému navýšení pro stabilitu oblouku.
Na obr. 2 je zachycen proces těsně před a po oddělení kapky svarového kovu z přídavného materiálu při tradičním MIG procesu. Proud během opětovného zapálení dosahuje až 150 A, výsledkem je pak nadměrný rozstřik. Vzhledem k základnímu materiálu je pak možno pozorovat mikrorozstřik, který se uchycuje na daném materiálu.
Při řízení tradičního MIG procesu je udávána pouze hodnota, zda je přídavný materiál „drát“ zkratován
pouze s ohledem na měřené napětí. Když je dosaženo zkratu, napětí je nízké vzhledem k odporu celého obvodu a při opětovném zapálení oblouku je napětí vysoké. Ze dvou základních důvodů tento princip měření je pro IAC nedostatečný: napětí je měřeno uvnitř svařovacího zdroje, a proto není reprezentující hodnotou napětí na oblouku. Kromě poklesu napětí na oblouku je měřen i úbytek napětí na kabelech v důsledku odporu a indukčnosti. S cílem snížení proudu při oddělením kapky je nezbytné předvídat vývoj celého procesu a ne pouze měřit napětí a vyhodnotit co se stalo v daném kroku. Opětovné zapálení oblouku je předpokládáno kontinuálním výpočtem průměru drátu při oddělení. Následující vztah vyjadřuje elektrické svorkové napětí zdroje oblouku:
Us = Lw . I + Rw . I + Re . I + UH
svorkové napětí při zkratu
Us = Lw . I + Rw . I + Re . I
Us - svorkové napětí dodávané svařovacím zdrojem
I - proud
Lw - indukčnost svařovacích kabelů
Rw – odpor svařovacích kabelů
Re – odpor elektrody
UH – úbytek napětí na oblouku
V případě známých hodnot proudu, napětí indukčnosti a odporu je možné vyjádřit úbytek napětí na oblouku, bez drahých externích měřících zařízen. Nicméně lze taktéž stanovit průměr drátu při oddělení přes nelineární funkci.
dtrad (x)=f(U,I,x)
Kde x je vektor popisující stav systému. Vzhledem k tomu, Že se hodnoty parametrů v průběhu času mění, jejich odhad Lw , Rw nebo UH se provádí rekurzivně z měření proudu a napětí.
Výsledek
Obr. 4 vyjadřuje měření napětí a proudu ve třech fázích cyklu standardním MIG procesem.
Obr. 5 zobrazuje tři fáze cyklu při svařování a kontrolou IAC procesu při stejných parametrech,
jako tradiční proces. Srovnáme-li oba průběhy je patrné, že při použití IAC je proudový průběh na hodnotě 250 A oproti 150 A u tradičního procesu, to zabezpečuje vyšší množství energie ve fázi zkratu a nižší energii využitou na hoření oblouku.
Pak je možné vyjádřit vnesené teplo ze vztahu:
H= U.I /v
H - vnesené teplo J/mm
U - napětí na oblouku
I - proud
v - rychlost svařování m/s
Při laboratorních testech byl použit svařovací hořák umístěný na lineárním pojezdu. Cílem bylo vyjádřit vnesené teplo při různých podávacích rychlostech a dalších parametrech ve srovnání IAC a tradičního zkratového procesu. V tabulce 1 jsou uvedeny naměřené hodnoty při svařovací rychlosti 0,25m/min. Tabulka 2 vyjadřuje naměřené hodnoty při rychlosti svařování 0,5m/min. Vypočítané vnesené teplo je znázorněné na obr. 6.
Při laboratorních testech byl použit svařovací hořák umístěný na lineárním pojezdu. Cílem bylo vyjádřit vnesené teplo při různých podávacích rychlostech a dalších parametrech ve srovnání IAC a tradičního zkratového procesu. V tabulce 1 jsou uvedeny naměřené hodnoty při svařovací rychlosti 0,25m/min. Tabulka 2 vyjadřuje naměřené hodnoty při rychlosti svařování 0,5m/min. Vypočítané vnesené teplo je znázorněné na obr. 6. Z tabulky 1, 2 a grafického znázornění obr. 6 jasně plyne podíl vneseného tepla při porovnání IAC a tradičního procesu. IAC tak zabezpečuje nižší vnesené teplo, jak je patrné, vnesené teplo je relativně konstantní okolo 20 J/mm, což způsobuje zlepšení v rozsahu od 15 do 30 % pro
nižší podávací rychlosti. Proces oddělení kapky vychází ze statutu změny napětí z nízkého na vysoké. Jak je možné vizuálně pozorovat na obrázku 4, 5, proudová hodnota pro oddělení kapky je podstatně nižší při použití systému IAC. Tabulka 1, 2 a obr. 7 jasně definuje naměřené hodnoty při opětovném
zapálení oblouku. Pro proces IAC jsou hodnoty konstantní okolo 40 A.V případě tradičního řízení
znovu zapálení oblouku lze pozorovat rostoucí lineární průběh v závislosti na podávací rychlosti.
Nízká proudová hladina při procesu oddělení kapky se systémem IAC rovněž eliminuje rozstřik
kovu uplývající na povrchu svarku.
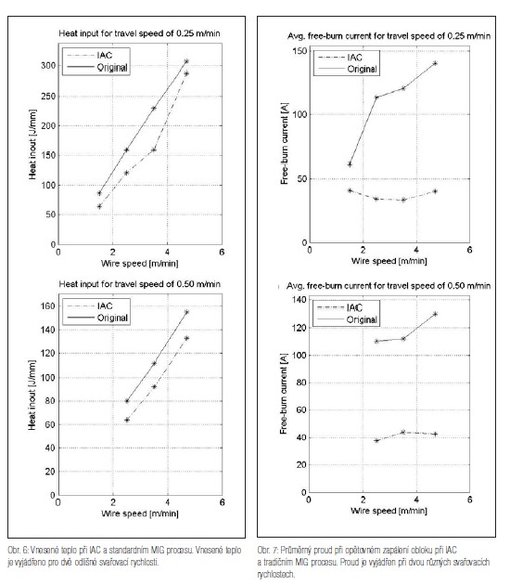
- Novinky
- Tipy, rady, doporučení
- Autoopravárenství
- Svařování ve výrobě
- Automatizace
- Robotizace
- Ocenění / Napsali o nás
- Výstavy